TESTING SERVICES

About HALT Testing
HALT (Highly Accelerated Life Testing) is an accelerated reliability test method designed to precipitate failures in a products design by subjecting the product to stresses well beyond its intended operating limits.
Overstressing = Accelerating Time.
Thermal and Vibration stresses are applied in a controlled, systematic fashion beginning with the least destructive stress (cold step) and progressing to the most destructive stress (combined thermal and vibration). The five phases of HALT are as follows:
- Cold Step
- Hot Step
- Rapid Thermal Cycling
- Vibration Step
- Combined Rapid Thermal Cycling & Vibration
At the conclusion of each phase, operating limits are determined. Operating limits are defined as follows: A stress level prior to where one or more of the products operating characteristics are no longer within specification. The product recovers when the stress is reduced to the prior passing level. Operating limits defined in the cold step and hot step phases are used to determine the Rapid Thermal Cycling profile. Results of the Vibration Step phase combined with the Rapid Thermal Cycling profile determine the Combined Rapid Thermal Cycling and Vibration profile.
Temperature and Vibration data are recorded throughout the HALT process. Failure modes are documented during each phase of HALT and correlated with the temperature and vibration data. This data is used to determine the weak links to fix, through the post HALT activities.
Post HALT activities should include:
- Root Cause Analysis
- Corrective Action
- Verification HALT
- Product ECO’s
Results of a successful HALT:
- Improve product design margins
- Discover product failure modes
- Create a more robust design
- Establish HASS parameters
Test Report:
Our test reports begin with a test objective and a background of the HALT process, defining the key benefits and methodology behind the test. It follows with an executive summary highlighting the HALT results in a simple, easy to read format. The test process and test setup is defined, explaining test fixturing, a description of test equipment, data collection methods, and the test routine. Detailed results pages are provided in both text and graphical formats illustrating the test progression and descriptions of failure modes. The appendix sections provide photographs of the setup, and vibration plots. Typical HALT reports range from 20 to 30 pages.
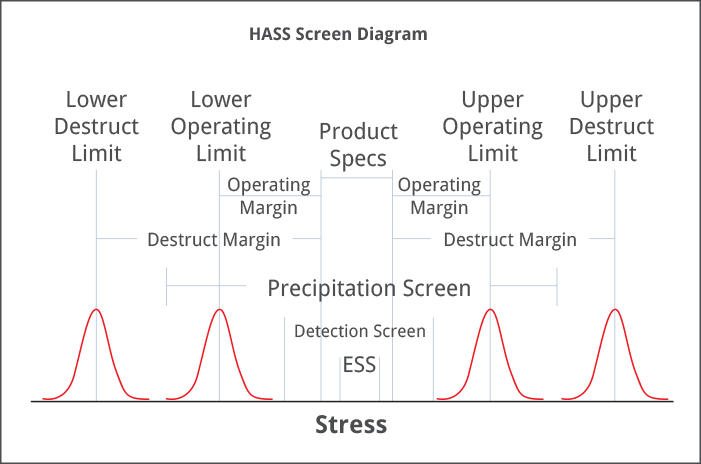
About HASS Screening
HASS (Highly Accelerated Stress Screening) is a manufacturing process that can replace long term Burn-in or ESS processes, saving time and money. HASS is typically a 2 to 4 hour screen, as compared to 12-24 hour ESS and 48-96 hour burn-in. HASS utilizes a combined thermal cycling and vibration profile, beyond the operating specifications of the product to accelerate failure in marginal products. Its intent is to expose process related variations in manufacturing, which cause the “out of box” infant failures that increase warranty costs.
HALT results are used to determine the starting point for HASS, and through a HASS development process (Proof of Screen and Proof of Life Evaluation), the final screen is determined.
About Temperature/Humidity Testing
Augment your HALT testing by utilizing our new ESPEC Temperature & Humidity chamber. Temperature & Humidity testing is an important step in product reliability, evaluating your products susceptibility to harsh conditions. Long soaks at high temperature & high humidity will provide a significant understanding of moisture penetration potential, allowing an investigation into how moisture affects the system in a conductive and material breakdown manner. Cycling from high temperature/high humidity to sub-freezing temperatures allows trapped moisture to freeze (and expand), thus potentially prying apart faulty materials that allowed moisture ingress. Failure modes commonly precipitated include defective package seals, faulty encapsulations, ineffective conformal coating, and dielectric failure caused by silver migration.